Health and Safety Issues When Working in a Factory
For those familiar with working in a factory environment, they’ll also be familiar with the hazards in and around their workplace. A hidden danger though comes when people become over familiar, they can become complacent and that’s when many accidents also can occur.
For that reason and especially when you are new to the environment, it’s important to be aware of health and safety issues when working in a factory. Here’s a checklist of some of the key hazards and issues, with some best practice ideas which may go help what you’re already doing.
Come on in and have a look at some of the health & safety issues.
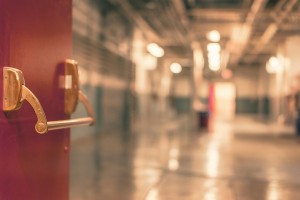
Someone Is New To The Factory And/Or The Job They’re Performing
Employees may suffer injury purely due to being unfamiliar with their machinery and workspace, or other hazards on site such as which walkways to use and where plant and machinery has right of way.
Speak to all employees and visiting contractors to make sure they’re aware of the latest risk assessments and protocol. Also reiterate with anyone who supervises an area or colleague so that the message is delivered twice. Not just supervisors but ALL employees need authority to challenge those working unsafely and stop work.
Slips And Trips
The most common health and safety issue. Even flooring which is kept clear, clean and tidy will help minimise the risk of slips and trips. It’s also vital that employees wear safety shoes which have anti-slip soles as opposed to just toe protection.
Vehicular Hazards
From pallet trucks and lifts, to delivery trucks and cars on the car park, the issues from an incident involving a vehicle and a pedestrian are potentially fatal. Walkways need to be clearly marked and kept clear at all times and copies of the routes should be readily available and well displayed, as well as issued to all employees and visiting contractors.
Reception staff should issue plans to all visitors on site.
Working At Height
The most dangerous health and safety issue is working at around ceiling height. My first project manager used to tell us all horror stories of the workers he’d seen fall from a head height platform and be unable to avoid landing on their head, neck or shoulders due to the short distance to impact.
Working platforms should be used correctly at all times. The risks are too great. Download the HSE guidance on work at height to check compliance.
Moving Heavy Objects
When transporting heavy object, it’s important to follow sensible lifting and manoeuvring techniques, but employers can reduce the risk of staff overloading themselves by providing carrying equipment which cannot be overloaded (such as trolleys and the like).
If the factory has machinery with large and/or heavy moving parts, all employees who could be present in the vicinity of the machine should undergo at least basic training, in case of an emergency situation.
Moving Parts Of Machinery
All moving parts which could cause harm – no matter how small – should be guarded to at least the manufacturer’s specification. The guards and protective equipment used should be checked at least once a month and work should cease immediately that a problem occurs or is noted.
Sharpening Tools
Time pressures or faulty equipment could lead to avoidable injuries when sharpening or maintaining tools. Beyond making sure only trained staff ever sharpen tools, there should always be a trained fitter available on site to make sure that, if the machine does falter, employees aren’t tempted to keep using a potentially dangerous machine.
Electricity
Shocks and burns are a potential health and safety issue from faulty or exposed electrical items. All appliances should be tested and certified safe and a planned maintenance inspection schedule of all machinery appliances should be undertaken.
Confined Space Working
A relatively uncommon health and safety issue but it is sometimes unavoidable and a number of people die from this issue each year in the UK. Working in enclosed spaces aren’t the only potential hazards; open chambers, vats, combustion chambers in a furnace, ductwork and even poorly ventilated rooms can soon become hazardous.
The first safety port of call is to avoid entering the confined space but if this is impossible, mitigate the risk of becoming trapped using only trained contractors who comply with the latest HSE guidelines on confined space working.
Asbestos Release During Maintenance
Usually well managed but nevertheless worth mentioning. Just always be sure to ensure signage is up to date and that only approved contractors interact with the material and fitters check conditions of it every two months.
Fire Routes
All staff and visitors should be aware of the current and latest fire escape routes and their muster points. Fire wardens should undergo training at least once a year and drills should be mandatory. Signage should be up to date, visible and in working order at all times.
Noise
Sound checks must be undertaken to make sure that general working conditions do not exceed safe levels. Ear plugs should be made a compulsory piece of PPE if level are higher than an average of 85 decibels. But it’s better practice to have them on offer regardless.
Noisy works should be kept to a minimum and breaks from the noise included, as well as fit and proper hearing protection for those nearby.
Heat Exposure
Although there is no legal maximum temperature. water, cool-down areas and regular breaks should be available to employees at all times when conditions are hot. If the heat is created from foundry type machinery, latest studies show that implementing Local Exhaust Ventilation and Respiratory Protective Equipment can help to ensure that employees are at least breathing clean and fresh air. This will reduce the risk of contracting disease and respiratory problems.
If working without mitigating these or any other health and safety issues is expected to be carried out – your factory simply isn’t safe and work should be stopped. The most efficient way of working safely is to make checks regularly and routinely, whilst fostering a culture that challenges unsafe working
Guest post written by Don Valley Engineering

A chartered (fellow) safety and risk management practitioner with 20+ years of experience. David provides a healthy dose of how-to articles, advice and guidance to make compliance easier for construction professionals, Architects and the built environment. Get social with David on Twitter and Linkedin.
2 Comments
My employer told me i have to tie my hair up after nine years working for them i dn not think it is a health risk it is just below shoulder length and it is not near the air tools that I use
Hi Susan. Thanks for dropping by. What tasks are you undertaking at work?